-
Other audit services
We help clients with the application and use of foreign financial aid of EU and other funds and help prepare financial reports.
-
Audit calculator
The calculator will answer if the company's sales revenue, assets or number of employees exceed the limit of an inspection or audit.
-
Payroll and related services
We perform payroll accounting for companies whether they employ a few or hundreds of employees.
-
Tax accounting
Grant Thornton Baltic's experienced tax specialists support accountants and offer reasonable and practical solutions.
-
Reporting
We prepare annual reports in a timely manner. We help to prepare management reports and various mandatory reports.
-
Consolidation of financial statements
Our experienced accountants and advisors help you prepare consolidation tables and make the consolidation process more efficient.
-
Consultancy and temporary staff
Our experienced specialists advise on more complex accounting transactions, rectify poor historic accounting, and offer the temporary replacement of an accountant.
-
Outsourced CFO service
Our CFO service is suitable for companies of all sizes and in all industries. We offer services to our clients in the required amount and competences.
-
Assessment of accounting processes
We help companies to implement accounting practices that are in compliance with local and international standards.
-
Accounting services for small businesses
We offer affordable service for small businesses. We help organize processes as smartly and cost-effectively as possible.
-
Cryptocurrency accounting
We keep up with blockchain technology to serve and advise crypto companies. We are supported by a network of colleagues in 130 countries.
-
Trainings and seminars
Our accountants have experience in all matters related to accounting and reporting. We offer our clients professional training according to their needs.
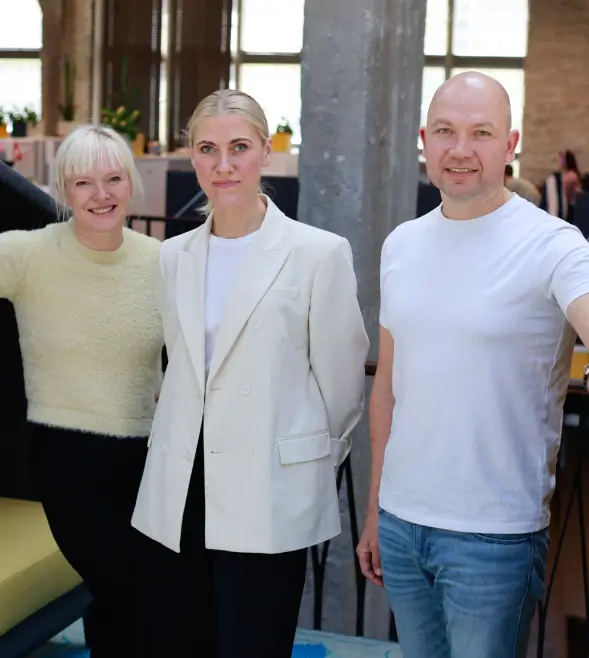
-
Business advisory
We offer legal support to both start-ups and expanding companies, making sure that all legal steps are well thought out in detail.
-
Fintech advisory
Our specialists advise payment institutions, virtual currency service providers and financial institutions.
-
Corporate advisory
We advise on legal, tax and financial matters necessary for better management of the company's legal or organizational structure.
-
Transaction advisory
We provide advice in all aspects of the transaction process.
-
Legal due diligence
We thoroughly analyze the internal documents, legal relations, and business compliance of the company to be merged or acquired.
-
In-house lawyer service
The service is intended for entrepreneurs who are looking for a reliable partner to solve the company's day-to-day legal issues.
-
The contact person service
We offer a contact person service to Estonian companies with a board located abroad.
-
Training
We organize both public trainings and tailor made trainings ordered by clients on current legal and tax issues.
-
Whistleblower channel
At Grant Thornton Baltic, we believe that a well-designed and effective reporting channel is an efficient way of achieving trustworthiness.
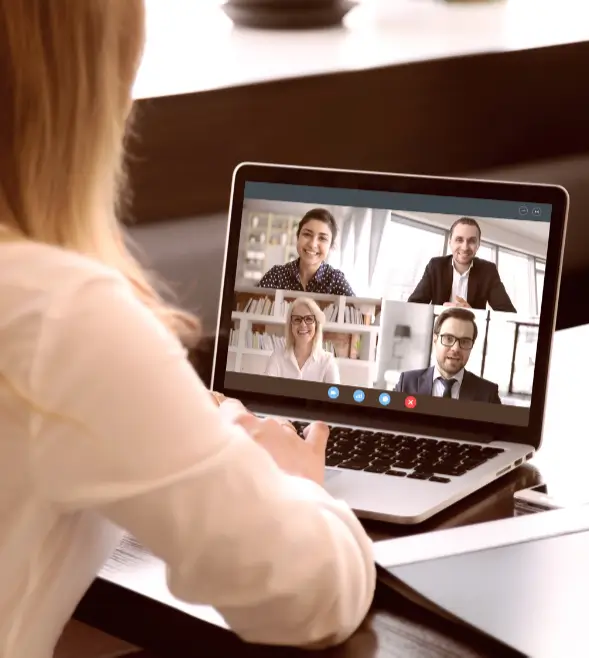
-
Business model or strategy renewal
In order to be successful, every company, regardless of the size of the organization, must have a clear strategy, ie know where the whole team is heading.
-
Marketing and brand strategy; creation and updating of the client management system
We support you in updating your marketing and brand strategy and customer management system, so that you can adapt in this time of rapid changes.
-
Coaching and development support
A good organizational culture is like a trump card for a company. We guide you how to collect trump cards!
-
Digital services
Today, the question is not whether to digitize, but how to do it. We help you develop and implement smart digital solutions.
-
Sales organisation development
Our mission is to improve our customers' business results by choosing the right focuses and providing a clear and systematic path to a solution.
-
Business plan development
A good business plan is a guide and management tool for an entrepreneur, a source of information for financial institutions and potential investors to make financial decisions.
-
Due diligence
We perform due diligence so that investors can get a thorough overview of the company before the planned purchase transaction.
-
Mergers and acquisitions
We provide advice in all aspects of the transaction process.
-
Valuation services
We estimate the company's market value, asset value and other asset groups based on internationally accepted methodology.
-
Forensic expert services
Our experienced, nationally recognized forensic experts provide assessments in the economic and financial field.
-
Business plans and financial forecasts
The lack of planning and control of cash resources is the reason often given for the failure of many businesses. We help you prepare proper forecasts to reduce business risks.
-
Outsourced CFO service
Our CFO service is suitable for companies of all sizes and in all industries. We offer services to our clients in the required amount and competences.
-
Reorganization
Our experienced reorganizers offer ways to overcome the company's economic difficulties and restore liquidity in order to manage sustainably in the future.
-
Restructuring and reorganisation
We offer individual complete solutions for reorganizing the structure of companies.
-
Corporate taxation
We advise on all matters related to corporate taxation.
-
Value added tax and other indirect taxes
We have extensive knowledge in the field of VAT, excise duties and customs, both on the national and international level.
-
International taxation
We advise on foreign tax systems and international tax regulations, including the requirements of cross-border reporting.
-
Transfer pricing
We help plan and document all aspects of a company's transfer pricing strategy.
-
Taxation of transactions
We plan the tax consequences of a company's acquisition, transfer, refinancing, restructuring, and listing of bonds or shares.
-
Taxation of employees in cross-border operations
An employee of an Estonian company abroad and an employee of a foreign company in Estonia - we advise on tax rules.
-
Tax risk audit
We perform a risk audit that helps diagnose and limit tax risks and optimize tax obligations.
-
Representing the client in Tax Board
We prevent tax problems and ensure smooth communication with the Tax and Customs Board.
-
Taxation of private individuals
We advise individuals on personal income taxation issues and, represent the client in communication with the Tax and Customs Board.
-
Pan-Baltic tax system comparison
Our tax specialists have prepared a comparison of the tax systems of the Baltic countries regarding the taxation of companies and individuals.
-
Internal audit
We assist you in performing the internal audit function, performing internal audits and advisory work, evaluating governance, and conducting training.
-
Internal Audit in the Financial Services Sector
We provide internal audit services to financial sector companies. We can support the creation of an internal audit function already when applying for a sectoral activity license.
-
Audit of projects
We conduct audits of projects that have received European Union funds, state aid, foreign aid, or other grants.
-
Prevention of money laundering
We help to prepare a money laundering risk assessment and efficient anti-money laundering procedures, conduct internal audits and training.
-
Risk assessment and risk management
We advise you on conducting a risk assessment and setting up a risk management system.
-
Custom tasks
At the request of the client, we perform audits, inspections and analyzes with a specific purpose and scope.
-
External Quality Assessment of the Internal Audit Activity
We conduct an external evaluation of the quality of the internal audit or provide independent assurance on the self-assessment.
-
Whistleblowing and reporting misconduct
We can help build the whistleblowing system, from implementation, internal repairs and staff training to the creation of a reporting channel and case management.
-
Information security management
We provide you with an information security management service that will optimise resources, give you an overview of the security situation and ensure compliance with the legislation and standards.
-
Information security roadmap
We analyse your organisation to understand which standards or regulations apply to your activities, identify any gaps and make proposals to fix them.
-
Internal audit of information security
Our specialists help detect and correct information security deficiencies by verifying an organization's compliance with legislation and standards.
-
Third party management
Our specialists help reduce the risks associated with using services provided by third parties.
-
Information security training
We offer various training and awareness building programmes to ensure that all parties are well aware of the information security requirements, their responsibilities when choosing a service provider and their potential risks.
-
Digital Operational Resilience Act (DORA)
We will help you create a DORA implementation model that meets your company's needs and ensures that you meet the January 2025 deadline.
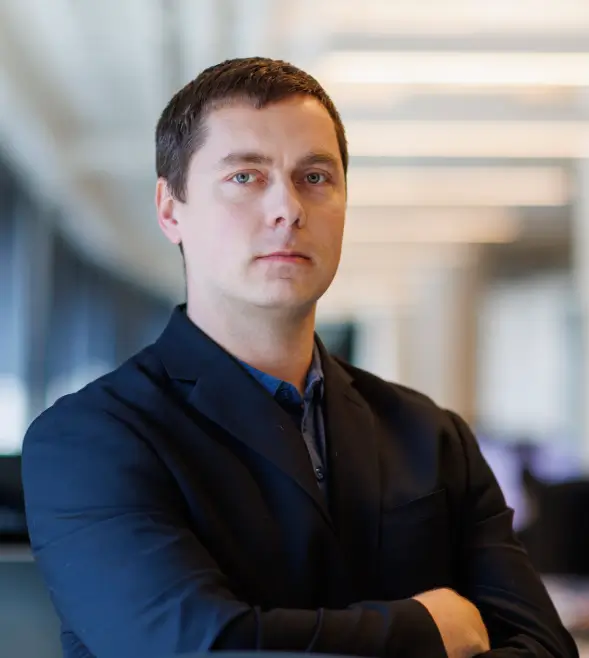
-
ESG advisory
We help solve issues related to the environment, social capital, employees, business model and good management practices.
-
ESG audit
Our auditors review and certify sustainability reports in line with international standards.
-
Sustainable investments
We help investors conduct analysis of companies they’re interested in, examining environmental topics, corporate social responsibility and good governance practices.
-
Sustainable tax behaviour
Our international taxation specialists define the concept of sustainable tax behaviour and offer services for sustainable tax practices.
-
ESG manager service
Your company doesn’t necessarily need an in-house ESG manager. This role can also be outsourced as a service.
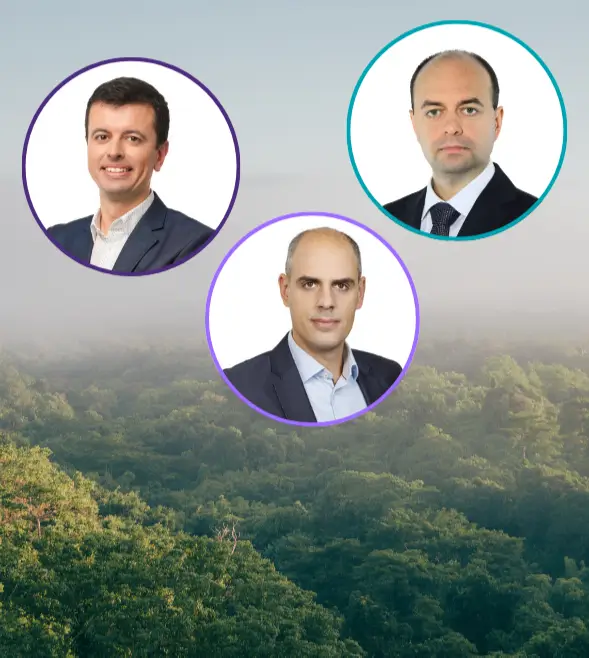
-
Recruitment services – personnel search
We help fill positions in your company with competent and dedicated employees who help realize the company's strategic goals.
-
Recruitment support services
Support services help to determine whether the candidates match the company's expectations. The most used support services are candidate testing and evaluation.
-
Implementation of human resource management processes
We either assume a full control of the launch of processes related to HR management, or we are a supportive advisory partner for the HR manager.
-
Audit of HR management processes
We map the HR management processes and provide an overview of how to assess the health of the organization from the HR management perspective.
-
HR Documentation and Operating Model Advisory Services work
We support companies in setting up HR documentation and operational processes with a necessary quality.
-
Employee Surveys
We help to carry out goal-oriented and high-quality employee surveys. We analyse the results, make reports, and draw conclusions.
-
HR Management outsourcing
We offer both temporary and permanent/long-term HR manager services to companies.
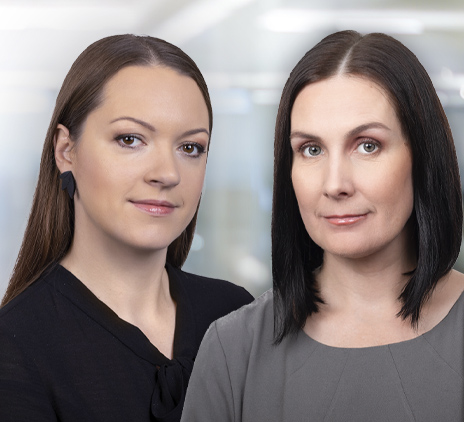
-
Digital strategy
We help assess the digital maturity of your organization, create a strategy that matches your needs and capabilities, and develop key metrics.
-
Intelligent automation
We aid you in determining your business’ needs and opportunities, as well as model the business processes to provide the best user experience and efficiency.
-
Business Intelligence
Our team of experienced business analysts will help you get a grip on your data by mapping and structuring all the data available.
-
Cybersecurity
A proactive cyber strategy delivers you peace of mind, allowing you to focus on realising your company’s growth potential.
-
Innovation as a Service
On average, one in four projects fails and one in two needs changes. We help manage the innovation of your company's digital solutions!
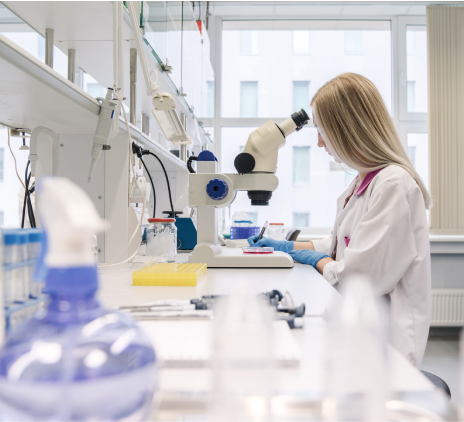
The end of the year is nearing and preparations for stock-taking or physical inventory are gaining momentum at companies. It often seems that checking inventories properly and smoothly is merely a nuisance for accountants, a job that gets in the way of the company’s usual activities for a few hours or days. But actually, stock-taking isn’t only the accountant’s concern: by placing emphasis on the important things, stock-taking can be organised more efficiently and reasonably.
The requirements for performing a physical inventory are set out in the Accounting Act and the public sector’s financial reporting guidelines, but the bulk of the material is found in internal regulations (accounting policies and procedures and other internal procedures etc.). Every organisation is different in terms of its stocks and assets, which makes it important to document the principles of warehouses and stock-taking in internal documents.
Stock-taking helps:
- make sure that inventories/assets exist
- compare the inventories/assets with financial accounting data
- document surpluses or deficits in stocks and correct data
- determine whether the conditions for storage and use of inventories are fulfilled or not
- detect any deficiencies and fraud
Stock-taking quality depends on preparation for and performing of the physical inventory. In the following, I will provide an overview of what to devote attention to while performing it.
15 guidelines for stock-taking
- Selecting the date for stock-taking. The farther away from the balance sheet date the physical inventory is performed, the greater the risk that there will be discrepancies in the period between the inventory count and the balance sheet date. The date is also important in light of the organisation's level of activity, as constant turnover of goods makes it harder to perform a count.
- Warehouse condition. Goods must be properly kept, guarded and their storage conditions guaranteed. A disorganised warehouse makes it harder to perform an inventory count, increases the risk of counting errors and complicates everyday warehouse movements.
Similar items should be located in the same location. If different locations need to be used, one should make sure that information is known to the staff involved in stock-taking (location-based). During the inventory count, spoiled, damaged or unfit inventories must also be documented. - Movements of goods during stock-taking. There should be no movements of inventory items during stock-taking. If this cannot be avoided, the incoming and outgoing goods should be factored in. Note: Movements between warehouses also affect the counting process.
- External warehouses.Stock-taking must include all of the company’s warehouses and locations, including external warehouses and goods held by other parties.
- Goods with a different owner. Goods with a different owner must be clearly separated from the organisation’s/company’s own merchandise to prevent errors in the inventory.
- Familiarity with the goods being inventoried. The staff conducting the physical inventory must be familiar with the merchandise (similar articles must not be confused). This reduces the risk of counting errors and fraud. A person responsible for the goods may simply show the counters the wrong item.
- Sequence in which inventories are counted. Goods must be inventoried in physical sequence (i.e. based on the principle of wall to wall). If this is not possible or efficient, a different principle for counting should be established.
- Marking counted goods. To avoid double-counting or leaving goods uncounted, the goods that have already been counted must clearly be marked.
- Stock-taking method. Weighing, measurement and counting must all be reliable. If the counting does not take place by piece, but rather on a different basis, the principles must be documented and as specific as possible. If needed, consider including specialists in the process.
- Accounting for sealed packages. If it is not expedient to count the contents of a sealed package piece by piece, the principle must be documented in internal instructions. The organisation/company must have certainty that the sealed packages are not empty.
- Manual counts vs. scanning codes. If a scanner is used, that does not mean that barcodes are necessarily correct (a comparison must be performed with the label/product). If the goods are manually counted, the person may accidentally record the wrong quantity or mix up articles. Scanning is certainly more automated and the risk of counting errors is lower.
- Counting sheets. The document used to tabulate the results of the count must not include the book balance of inventories. This will reduce the possibility of manipulation of results.
- Filling in the counting sheets. Inventory data must be entered into lists indelibly to minimise the possibility of manipulating results. Corrections to the lists must be made by striking out an entry, and if scanners are used, by adding a correction row.
- Checking and supervising the work of the stock-taking staff. The stock-taking committee must be as independent as possible yet familiar with the goods. In order to simplify the inventory checking, the person responsible for the goods in stock must be present for the counting so that they can assist if necessary. The counting process must be controlled and controllable. At the end of the inventory count, all counting sheets must be gathered up.
- Larger discrepancies than expected. Counting errors can be avoided by using parallel counting performed by a team consisting of multiple members. If there are too many errors, a new inventory must be organised.
Stock-taking does not end with a count
At the end of a physical inventory, differences between the financial accounting data and the actual balance usually occur. Consequently, the stock-taking is not over yet; it should be followed by an analysis of the result. But in an organisation where activity is coordinated the differences cannot be shockingly great.
Natural losses also occur depending on the organisation’s field and specifics. When goods come in and go out, articles may become mixed up or some items can go missing during the production process. Nor are arithmetic errors ruled out during counting. Many of the people who have served on stock-taking committees have become smarter due to their experience. Such aspects learned include the need for numbering counting sheets before starting the inventory. Following such rules will prevent resource-intensive errors.
If the results seem unnatural with discrepancies that are unjustifiably large, this points to poor quality of stock accounting or the stock-taking itself. Visit the following article to learn about how fraud and theft is detected during stock-taking.
If stock-taking was performed in a substandard manner, the need to perform a second stock-taking needs to be considered. Stock accounting should take place every day to ensure that the inventory count serves the purpose of verification, not accounting.