-
Other audit services
We help clients with the application and use of foreign financial aid of EU and other funds and help prepare financial reports.
-
Audit calculator
The calculator will answer if the company's sales revenue, assets or number of employees exceed the limit of an inspection or audit.
-
Payroll and related services
We perform payroll accounting for companies whether they employ a few or hundreds of employees.
-
Tax accounting
Grant Thornton Baltic's experienced tax specialists support accountants and offer reasonable and practical solutions.
-
Reporting
We prepare annual reports in a timely manner. We help to prepare management reports and various mandatory reports.
-
Consolidation of financial statements
Our experienced accountants and advisors help you prepare consolidation tables and make the consolidation process more efficient.
-
Consultancy and temporary staff
Our experienced specialists advise on more complex accounting transactions, rectify poor historic accounting, and offer the temporary replacement of an accountant.
-
Outsourced CFO service
Our CFO service is suitable for companies of all sizes and in all industries. We offer services to our clients in the required amount and competences.
-
Assessment of accounting processes
We help companies to implement accounting practices that are in compliance with local and international standards.
-
Accounting services for small businesses
We offer affordable service for small businesses. We help organize processes as smartly and cost-effectively as possible.
-
Cryptocurrency accounting
We keep up with blockchain technology to serve and advise crypto companies. We are supported by a network of colleagues in 130 countries.
-
Trainings and seminars
Our accountants have experience in all matters related to accounting and reporting. We offer our clients professional training according to their needs.
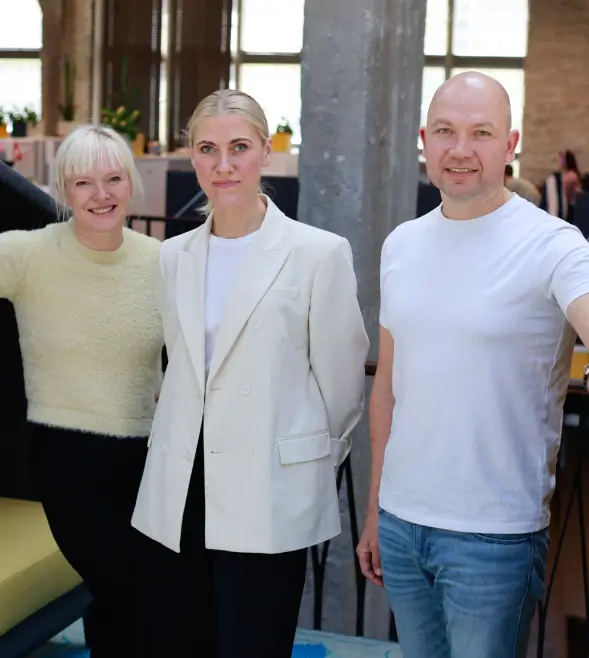
-
Business advisory
We offer legal support to both start-ups and expanding companies, making sure that all legal steps are well thought out in detail.
-
Fintech advisory
Our specialists advise payment institutions, virtual currency service providers and financial institutions.
-
Corporate advisory
We advise on legal, tax and financial matters necessary for better management of the company's legal or organizational structure.
-
Transaction advisory
We provide advice in all aspects of the transaction process.
-
Legal due diligence
We thoroughly analyze the internal documents, legal relations, and business compliance of the company to be merged or acquired.
-
In-house lawyer service
The service is intended for entrepreneurs who are looking for a reliable partner to solve the company's day-to-day legal issues.
-
The contact person service
We offer a contact person service to Estonian companies with a board located abroad.
-
Training
We organize both public trainings and tailor made trainings ordered by clients on current legal and tax issues.
-
Whistleblower channel
At Grant Thornton Baltic, we believe that a well-designed and effective reporting channel is an efficient way of achieving trustworthiness.
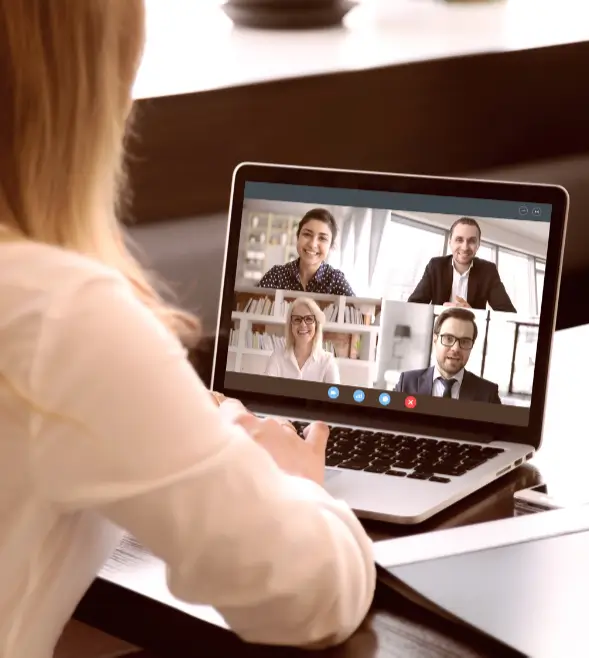
-
Business model or strategy renewal
In order to be successful, every company, regardless of the size of the organization, must have a clear strategy, ie know where the whole team is heading.
-
Marketing and brand strategy; creation and updating of the client management system
We support you in updating your marketing and brand strategy and customer management system, so that you can adapt in this time of rapid changes.
-
Coaching and development support
A good organizational culture is like a trump card for a company. We guide you how to collect trump cards!
-
Digital services
Today, the question is not whether to digitize, but how to do it. We help you develop and implement smart digital solutions.
-
Sales organisation development
Our mission is to improve our customers' business results by choosing the right focuses and providing a clear and systematic path to a solution.
-
Business plan development
A good business plan is a guide and management tool for an entrepreneur, a source of information for financial institutions and potential investors to make financial decisions.
-
Due diligence
We perform due diligence so that investors can get a thorough overview of the company before the planned purchase transaction.
-
Mergers and acquisitions
We provide advice in all aspects of the transaction process.
-
Valuation services
We estimate the company's market value, asset value and other asset groups based on internationally accepted methodology.
-
Forensic expert services
Our experienced, nationally recognized forensic experts provide assessments in the economic and financial field.
-
Business plans and financial forecasts
The lack of planning and control of cash resources is the reason often given for the failure of many businesses. We help you prepare proper forecasts to reduce business risks.
-
Outsourced CFO service
Our CFO service is suitable for companies of all sizes and in all industries. We offer services to our clients in the required amount and competences.
-
Reorganization
Our experienced reorganizers offer ways to overcome the company's economic difficulties and restore liquidity in order to manage sustainably in the future.
-
Restructuring and reorganisation
We offer individual complete solutions for reorganizing the structure of companies.
-
Corporate taxation
We advise on all matters related to corporate taxation.
-
Value added tax and other indirect taxes
We have extensive knowledge in the field of VAT, excise duties and customs, both on the national and international level.
-
International taxation
We advise on foreign tax systems and international tax regulations, including the requirements of cross-border reporting.
-
Transfer pricing
We help plan and document all aspects of a company's transfer pricing strategy.
-
Taxation of transactions
We plan the tax consequences of a company's acquisition, transfer, refinancing, restructuring, and listing of bonds or shares.
-
Taxation of employees in cross-border operations
An employee of an Estonian company abroad and an employee of a foreign company in Estonia - we advise on tax rules.
-
Tax risk audit
We perform a risk audit that helps diagnose and limit tax risks and optimize tax obligations.
-
Representing the client in Tax Board
We prevent tax problems and ensure smooth communication with the Tax and Customs Board.
-
Taxation of private individuals
We advise individuals on personal income taxation issues and, represent the client in communication with the Tax and Customs Board.
-
Pan-Baltic tax system comparison
Our tax specialists have prepared a comparison of the tax systems of the Baltic countries regarding the taxation of companies and individuals.
-
Internal audit
We assist you in performing the internal audit function, performing internal audits and advisory work, evaluating governance, and conducting training.
-
Internal Audit in the Financial Services Sector
We provide internal audit services to financial sector companies. We can support the creation of an internal audit function already when applying for a sectoral activity license.
-
Audit of projects
We conduct audits of projects that have received European Union funds, state aid, foreign aid, or other grants.
-
Prevention of money laundering
We help to prepare a money laundering risk assessment and efficient anti-money laundering procedures, conduct internal audits and training.
-
Risk assessment and risk management
We advise you on conducting a risk assessment and setting up a risk management system.
-
Custom tasks
At the request of the client, we perform audits, inspections and analyzes with a specific purpose and scope.
-
External Quality Assessment of the Internal Audit Activity
We conduct an external evaluation of the quality of the internal audit or provide independent assurance on the self-assessment.
-
Whistleblowing and reporting misconduct
We can help build the whistleblowing system, from implementation, internal repairs and staff training to the creation of a reporting channel and case management.
-
Information security management
We provide you with an information security management service that will optimise resources, give you an overview of the security situation and ensure compliance with the legislation and standards.
-
Information security roadmap
We analyse your organisation to understand which standards or regulations apply to your activities, identify any gaps and make proposals to fix them.
-
Internal audit of information security
Our specialists help detect and correct information security deficiencies by verifying an organization's compliance with legislation and standards.
-
Third party management
Our specialists help reduce the risks associated with using services provided by third parties.
-
Information security training
We offer various training and awareness building programmes to ensure that all parties are well aware of the information security requirements, their responsibilities when choosing a service provider and their potential risks.
-
Digital Operational Resilience Act (DORA)
We will help you create a DORA implementation model that meets your company's needs and ensures that you meet the January 2025 deadline.
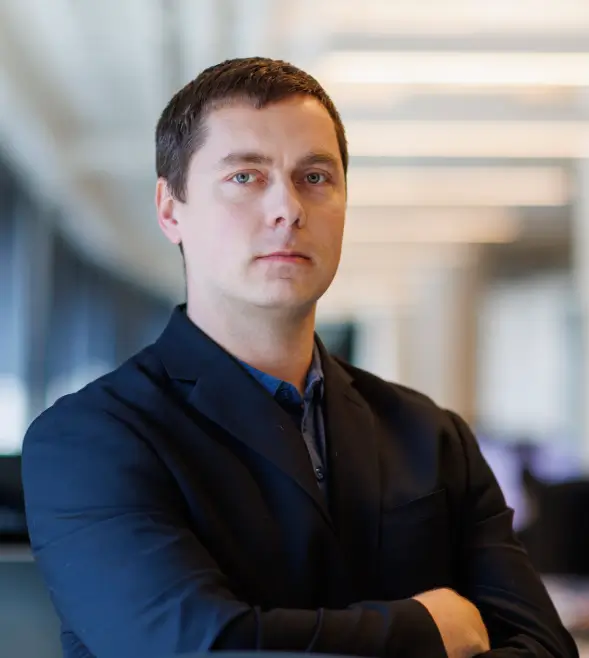
-
ESG advisory
We help solve issues related to the environment, social capital, employees, business model and good management practices.
-
ESG audit
Our auditors review and certify sustainability reports in line with international standards.
-
Sustainable investments
We help investors conduct analysis of companies they’re interested in, examining environmental topics, corporate social responsibility and good governance practices.
-
Sustainable tax behaviour
Our international taxation specialists define the concept of sustainable tax behaviour and offer services for sustainable tax practices.
-
ESG manager service
Your company doesn’t necessarily need an in-house ESG manager. This role can also be outsourced as a service.
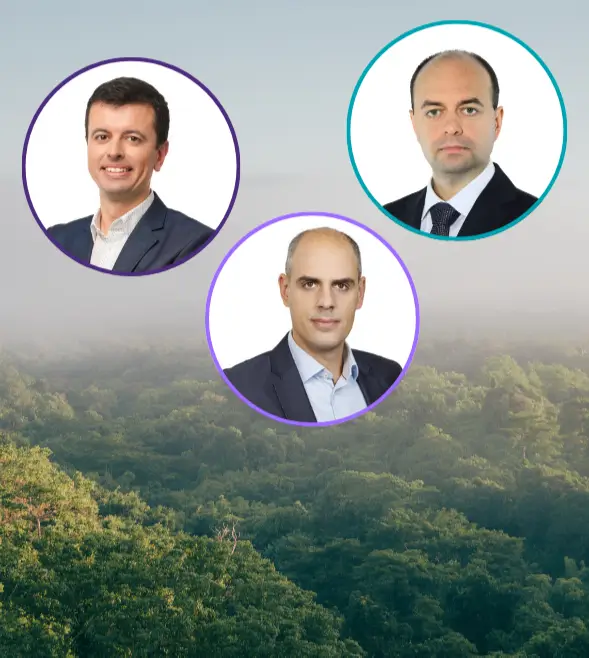
-
Recruitment services – personnel search
We help fill positions in your company with competent and dedicated employees who help realize the company's strategic goals.
-
Recruitment support services
Support services help to determine whether the candidates match the company's expectations. The most used support services are candidate testing and evaluation.
-
Implementation of human resource management processes
We either assume a full control of the launch of processes related to HR management, or we are a supportive advisory partner for the HR manager.
-
Audit of HR management processes
We map the HR management processes and provide an overview of how to assess the health of the organization from the HR management perspective.
-
HR Documentation and Operating Model Advisory Services work
We support companies in setting up HR documentation and operational processes with a necessary quality.
-
Employee Surveys
We help to carry out goal-oriented and high-quality employee surveys. We analyse the results, make reports, and draw conclusions.
-
HR Management outsourcing
We offer both temporary and permanent/long-term HR manager services to companies.
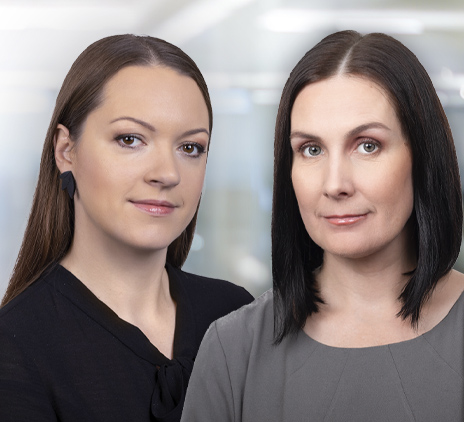
-
Digital strategy
We help assess the digital maturity of your organization, create a strategy that matches your needs and capabilities, and develop key metrics.
-
Intelligent automation
We aid you in determining your business’ needs and opportunities, as well as model the business processes to provide the best user experience and efficiency.
-
Business Intelligence
Our team of experienced business analysts will help you get a grip on your data by mapping and structuring all the data available.
-
Cybersecurity
A proactive cyber strategy delivers you peace of mind, allowing you to focus on realising your company’s growth potential.
-
Innovation as a Service
On average, one in four projects fails and one in two needs changes. We help manage the innovation of your company's digital solutions!
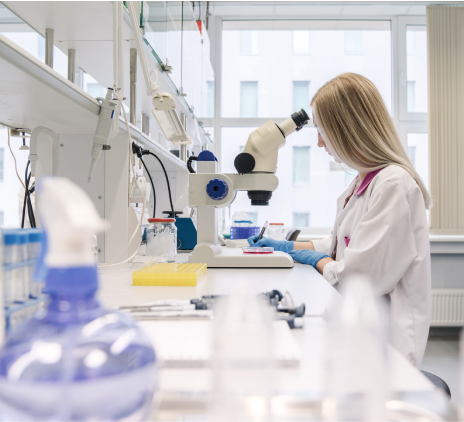
A stock-taking or physical inventory performed in a quality manner gives the heads of all units in a company assurance that financial statements and databases present a true and fair view of assets and inventories in stock. Periodic stock-taking is also quite effective for preventing fraud.
Thus, a physical inventory is one of the most important control procedures in the internal control toolbox and it is an endeavour that should be approached carefully.
Stock-taking can reduce risk of fraud
Stock-taking can also successfully be used as a part of internal control on a recurring basis, not just once a year. Random inventory checking exerts a disciplining effect and current warehouse accounting will likely become higher in quality. It is also good to sometimes use out-of-house partners to perform physical inventory in order to avoid conflicts of interest or resolve concerns over insufficient resources.
Counting mistakes is reduced by automating the process as much as possible. To keep the stock-taking results from being in the domain of the accountants and management alone, the establishment of financial incentives can also be considered. Proprietary liability for deficits or, the other way around, rewarding employees if there are only minimal discrepancies in unannounced inventory checks may prove very effective. Incidents of fraud can be established by constant analysis of stock-taking results and current accounting.
Physical inventories generally expose any theft
If warehouse accounting and physical inventories are performed correctly, any discrepancy will generally be traced to foul play. Discrepancies can stem from thefts of goods (including in small quantities) and recording of deficits to cover for skimming of goods. Even what appear to be minimal differences can conceal fraud if the inventory results have been manipulated or the goods have been falsified or counterfeited. For example, boxes might be empty or liquids may turn out to be ordinary tap water.
Fraud may or may not always be revealed in the course of an inventory. Thus, one should not rely solely on inventory – other internal control systems are also important for detecting fraud.
Condition of assets/goods in stock must also be assessed
When taking inventory, the condition of stored assets/stocks must also be evaluated. If the shelf life has expired, and this was not noticed during the stock-taking and the company’s logistics unit lacks information about this for whatever reason, these goods will end up being recognized on the balance sheet at the incorrect value.
Another important risk in production is the lack of high-quality raw material, although the company’s records indicate that there are materials in stock. Such a situation may lead to a production stoppage. Still, one should not forget the possibility that rodents, water damage and other factors may also worsen the value of goods in the warehouse or even contribute to a total loss of goods.
If the condition of goods is not carefully inspected in the course of a stock-taking, such incidents may go unnoticed. There is a very clear requirement in the state sector – assets and inventories not used must be written down and written off.